Choose Sleeve Labeling Equipment | sr-packing.com
Choosing the right sleeve labeling equipment is critical for achieving efficient, high-quality packaging while meeting your production goals. Below is a guide to help you select the best system for your needs:
Key Considerations When Selecting Sleeve Labeling Equipment
1. Container Type
Material: Glass, plastic, metal, or irregular shapes (e.g., tapered bottles, square jars).
Size: Diameter, height, and weight of containers.
Throughput: Production speed (containers per minute/hour).
2. Label Type
Shrink Sleeves: Requires heat tunnels for shrinking (PVC, PETG, OPS films).
Stretch Sleeves: Elastic labels applied without heat.
Tamper-Evident Sleeves: Adds security features.
3. Production Volume
Low- to Mid-Volume: Semi-automatic machines (ideal for startups or small batches).
High-Volume: Fully automatic systems with conveyor integration (e.g., rotary or inline applicators).
4. Automation Level
Manual/Semi-Auto: Operator-assisted loading; cost-effective for flexibility.
Fully Auto: Robotic handling, IoT connectivity, and minimal human intervention.
5. Sustainability Goals
Compatibility with recyclable/biodegradable films (e.g., rPETG, PLA).
Energy-efficient heat tunnels (e.g., infrared vs. steam).
6. Budget
Upfront costs vs. long-term ROI (consider maintenance, downtime, and material waste).
Types of Sleeve Labeling Equipment
1. Semi-Automatic Applicators
Best for: Small batches, product prototyping, or limited budgets.
Features: Manual container loading, basic heat tunnels, adjustable settings.
2. Fully Automatic Inline Systems
Best for: High-speed production (e.g., 200+ containers/minute).
Features: Integrated conveyors, auto-sleeve feeding, precision sensors.
3. Rotary Sleeve Applicators
Best for: Round containers (bottles, cans) at ultra-high speeds.
Features: Rotary carousel design, synchronized labeling, and shrinking.
4. Hybrid Machines
Best for: Multi-purpose operations (e.g., handles both shrink and stretch sleeves).
5. Tamper-Evident Systems
Best for: Pharmaceuticals or food packaging; adds perforations or seals.
Step-by-Step Selection Guide
1. Define Your Needs
List container specs, label material, daily output, and future scalability.
2. Prioritize Flexibility
Choose equipment that handles multiple container shapes/sizes if diversifying products.
3. Test Compatibility
Run trials with your containers and labels to check precision (e.g., sleeve placement, shrinkage).
4. Evaluate Energy Efficiency
Opt for machines with low-energy heat tunnels (e.g., infrared) to reduce operating costs.
5. Consider After-Sales Support
Ensure the supplier offers training, spare parts, and technical assistance.
6. Future-Proofing
Look for IoT-enabled machines with predictive maintenance and software updates.
Industries and Use Cases
Food & Beverage: High-speed rotary systems for bottles/cans.
Cosmetics: Precision applicators for luxury glass bottles.
Pharma: Tamper-evident systems with sterile compliance.
Chemicals: Durable labels for industrial drums.
Top Trends in Sleeve Labeling
Smart Packaging: Integration with QR codes or NFC tags via sleeve labels.
Eco-Friendly Solutions: Machines compatible with mono-material films (easier recycling).
AI-Driven Quality Control: Cameras detect misaligned sleeves or defects in real time.
Final Tips
Request Demos: Test equipment with your actual containers.
Calculate TCO: Factor in energy use, maintenance, and material savings.
Partner with Experts: Work with suppliers who understand your industry’s unique challenges.
By aligning your equipment choice with production demands, container specs, and sustainability goals, you can optimize efficiency, reduce waste, and create packaging that captivates consumers.
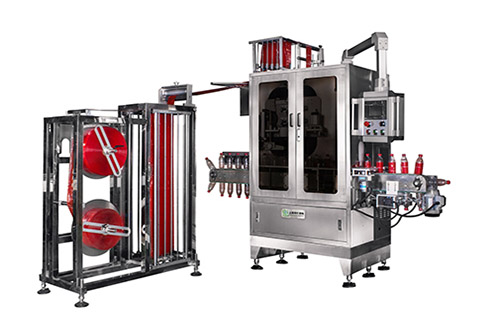